Installation of 115 000 m3/h efficiency dust collector for chipboard dust is about to be completed
Posted: 02.06.2021
Designing and producing new dust collecting devices, having new challanges ahead, complying with all legal requirements and standards together with a constant care over the environment and also keeping a high standard of the produced devices and services provided, have all become a great passion of ours.
Only a few hours have left to complete and start up our new EKO-FILTR dust collector, which is going to work for a fast developing company located in Wieruszów – a centre of furniture producers in Poland.
The newly installed filtrating device is for extracting dust from chipboard processing machines. The efficiency of the dust collector is designed for 115 000 m3/h and it has been designed as a compact device in order to take minimum space.
The dust collector is situated on a solid carrying construction under which 2 containers can be located for waste discharge. The containers are adapted for a specially designed pneumatic docking system – each container has got two openings. This solution minimizes the dust spread around the device to minimum.
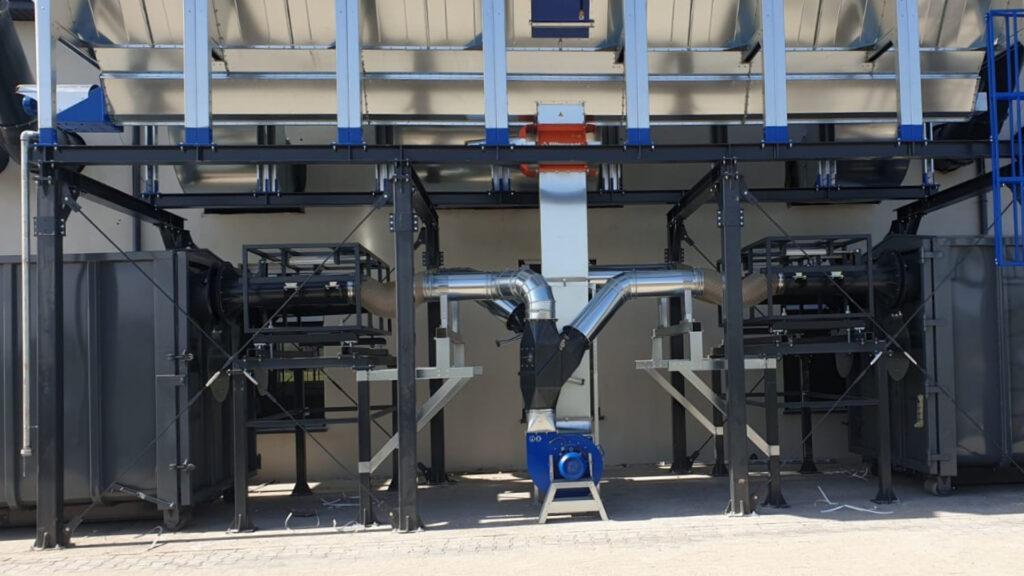
The exhaust fans are located inside the dust collector in its top part and they are going to work in pull pressure system. There are many advantages of such solution, here a few most important ones:
- saving space – the exhaust fans are located inside the dust collector in its top part – there is no need for additional foundations for free-standing fans, and the filtrating station can be located closer to the production hall which reduces the length of the pipe lines.
- reducing noise – the exhaust fans are as standard built in acoustic cabins thanks to which the noise generated during their work is minimized.
- extending service life of the devices and gaining lower energy consumption – the fans working in negative pressure ehaust clean air only (in effect there is no dust or other particles of dirt coming through the fans that could affect their internal parts). By the use of special rotors in the fans, their efficiency is higher and energy consumption is lower.
- cascade system of fans – inside the dust collector there are usuallly a few fans installed of the same or similar power. At a given time, and with a proper piping system only the required number of fans operate – that is, the number of fans that are needed for a given period of time and for the required efficiency. What is more, during inspection works, the fans which are not beeing serviced can still operate and exhaust the air.

Of course we have not forgotten to equip the entire system with explosion protection devices. It is well known that extracted dust mixed with air can create a potentially explosive atmosphere inside a filtrating device, therefore:
- all components and parts of the dust collector, both electrical and non electrical, that are inside a dust collector (thus operating in a potentially explosive atmosphere) have been designed for explosion hazard zones, adequately certified and labelled with Ex marking,
- the system is equipped with protective devices, which before they were introduced into the market, had to be subjected to rigorous testing at notified bodies. All the devices used in the presented dedusting system have been positively assessed and Ex certified. These are the following devices:
- explosion decompression panels – installed on the dirty side of the dust collector – work as explosion relief devices,
- flap valves – installed on the dirty air inlet ducting – work as explosion isolation,
- rotary valve – installed at the bottom part of the dust collector, which apart from pressure free transport of dust is also a device which isolated explosion.
The system which is designed and executed in the way described above is prepared for such dangerous situation as dust explosion. The body of the dust collector – made of 2 mm and 3 mm steel, is able to withstand explosion and the protecive devices are designed to minimize its effects in the following way:
- the wave and flame of the explosion are relieved and directed outside of the dust collector into the safe area
- the explosion wave and flame are prevented from spreading by the flap valves so the inlet ducting and working area are protected
- the rotary valve installed at the bottom of the dust collector stops the spread of explosion into the transporting system (from underneath the dust collector to the containers).